- Get link
- X
- Other Apps
DVN: Interview: Sumit Sharma, CEO of MicroVision
Interview: Sumit Sharma, CEO of MicroVision
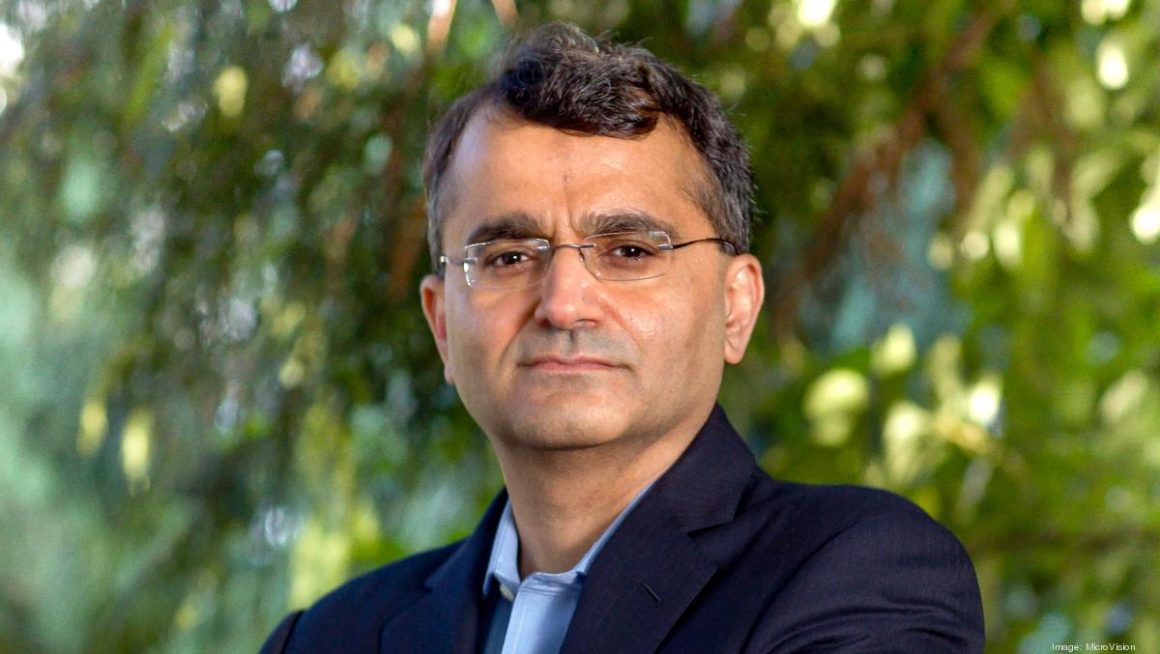
Sumit was appointed Chief Executive Officer and a member of the Board of Directors in February 2020. Sumit joined MicroVision in September 2015, overseeing the company’s engineering, operations, and R&D functions. Sumit has extensive background in high volume consumer electronics and automotive product development and launch. Sumit has held leadership positions in engineering and operations at Jawbone, Google, and MYVU Corporation. A patent holder, Sumit received a B.S. degree in mechanical engineering from the New Jersey Institute of Technology
DVN: Dear Sumit, thank you for giving us the opportunity for this interview. MicroVision is a high-tech company listed on the NASDAQ stock exchange. Can you give us a rough overview of the historical development of MicroVision?
Sumit: Thank you for the opportunity to share our story. MicroVision has a long history as a high-tech company. Our headquarters are based in Redmond Washington. We were founded in 1993 and in late 90’s went public. From the beginning MicroVision has focused on laser beam scanning MEMS technology. Our first product and customer base were the US military. So high reliability MEMS and systems design is part of our DNA for decades. We expanded our technology offering to cover consumer electronics products, gathering extensive experience in cost optimization for high tech products. MicroVision has been a key technology provider for global OEMs like Pioneer, Sony and Microsoft and a few others. We started our internal R&D for lidar product as early as 2011 and continuously invested to developing a differentiated product. As I became CEO, I focused the company on our automotive lidar product and now the company is focused on enabling L3 ADAS features with our lidar and software offering.
DVN: Some years ago, MicroVision decided to include also automotive lidar into its portfolio. What were the main considerations to establish this strategic move?
Sumit: During our more that 10 years of R&D investment in lidar, we developed some key intellectual property that would enable a long range, high resolution, and low latency lidar in a small form factor. Our lidar has innovative features like active scan locking for send and receive channels that allows us to have high signal to noise ratio in 100k lux, pixel by pixel Automatic Emissions Control (AEC) that enables Class 1 safety implements at unit level, pulse encoding that allows us to provide a secure streaming lidar and of course object level software interface that OEM require. This is context.
Since we have a differentiated product, we decided to expand from being a technology supplier and provide a fully designed system which we have experience with. We believe to be successful in this space we need to dedicate all our financial and technical resources to the automotive space and establish ourselves as a Hardware and Software ADAS Tier 1 supplier to Automotive OEM and Integration Tier 1.
DVN: MicroVision just launched its latest automotive product MAVIN DR Dynamic View Lidar at the recent Autosens in Brussels. What were the reactions on your product offer?
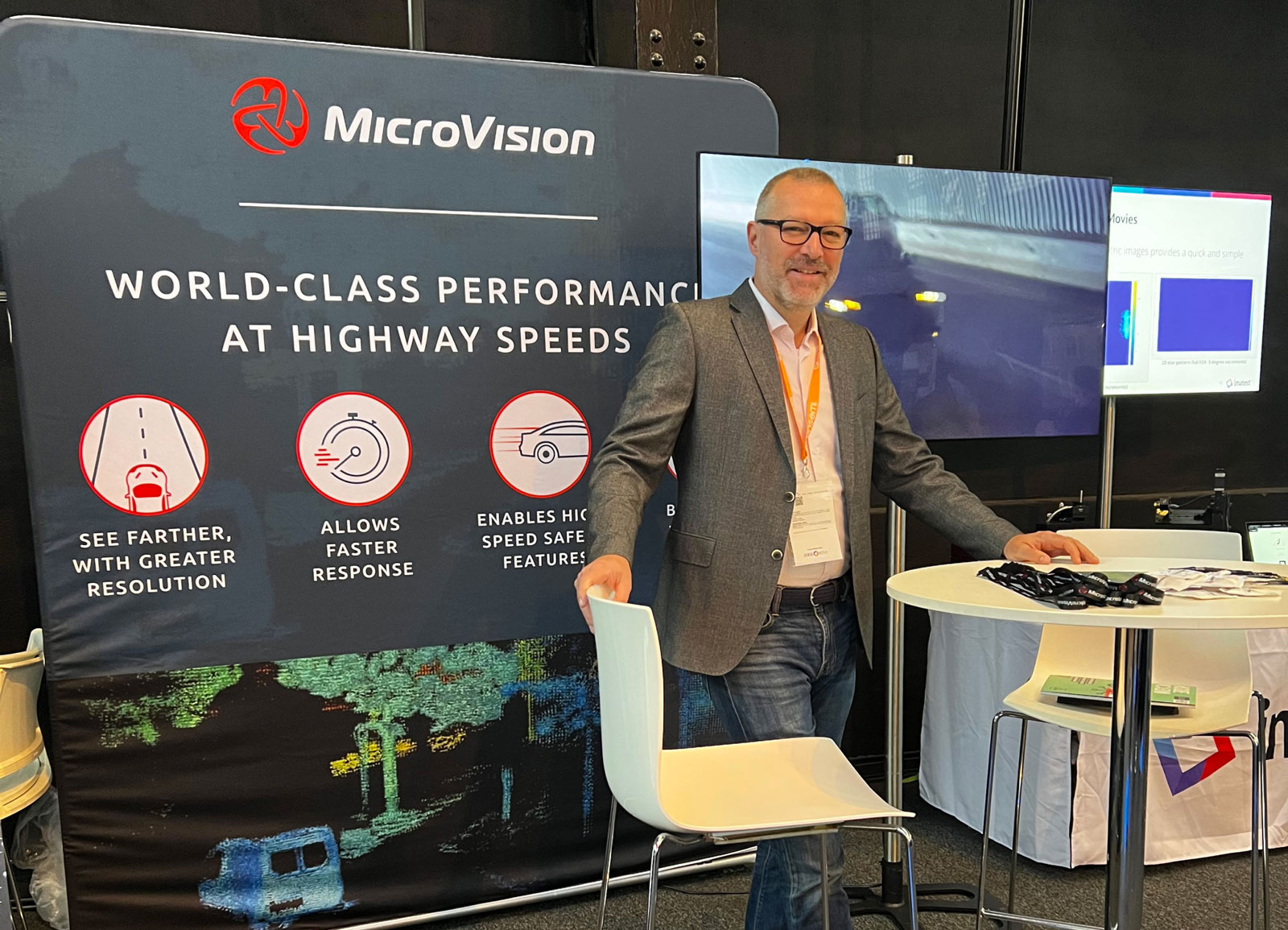
Sumit: The reaction to the product introduction has been positive. We have MAVIN mounted on our demo vehicle in Germany and have had the opportunity to showcase it to OEM and Tier one in Europe. The response to the quality of the lidar and construction of the hardware has been very positive, and we move along in our engagements with interested parties.
DVN: MicroVision is working with MEMS based solid-state lidar technology. What is setting your technology apart from your competition in the automotive field? Can you mention some key specifications, engineering elements or application advantages?
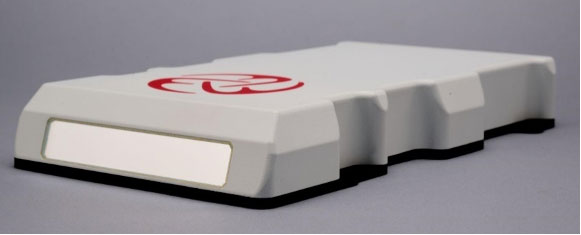
Sumit: Lets discuss this in two discussion streams.
First, the key features of our technology are dynamic field of view with 100-degrees near field, 50-degrees mid-field and 25-degrees far field of view in the same lidar product, with a 200+ meter range we also have 0.04-degree vertical angular resolution through the entire field. All these specifications delivered at streaming 30 hertz point cloud. Each position in the point cloud would also be able to provide dual returns. The sensor also outputs 8-bit intensity of each pixel as well as axial and radial velocity of clusters. These features are delivered in a low-profile sensor ideal for roofline mounting with a visible aperture window less than 14 millimetres tall in our A-sample. And of course, one of the outstanding features is the pixel-by-pixel class 1 safety provided from within the lidar sensor which will further enhance OEM system functional safety.
Secondly, these features are enabled by MEMS running in non-resonating mode, active scan locked between transmit and receive side. The system utilizes our custom MEMS module based on 905 nm laser from a prominent German laser partner. Consecutively emitted laser pulses are coded in flight to achieve the point cloud density as well as provide immunity from other lidars operating at target wavelength. All this including our class 1 and object interface (driveable/non-driveable) running from our custom digital ASIC. I am very proud of our team to achieve this.
DVN: Some more detailed technical questions. Which wavelength range have you chosen for MAVIN DR? What are the reasons for this choice?
Sumit: We have chosen 905 nm multi-mode laser diode as our technology node for this component. With the extremely high automotive reliability and wide performance range required for a system like this, we chose to pick the most mature and tested laser wavelength available in market by one of the most trusted companies in laser field.
This laser coupled with our intellectual property of active scan locked MEMS and unique pulsing sequence, we can achieve the range and immunity to sunlight and other lidar. Additionally, our choice provides for the lowest expected power for the system. We are certain this is the right choice for our technology since it will dominate the lidar future.
DVN: The power consumption of lidar systems is estimated to be 7-10 Watts per lidar sensor. This is comparable to the consumption of a simple LED headlight. Will power consumption become a key criterion for application of lidar sensors?
Sumit: Power is always key for any system in automobile given the potential requirements of 105 C case temperature that will come for roofline mounting. We provide “smart pulsing” option to our customer as a one-time programmable feature that will allow power reductions. But the main power reduction comes for implementing our system in an ASIC form factor. Our choice of laser wavelength also provides the range with reduced power.
Smart pulsing is basically, within the field of views customer define regions that they do not require full pulsing, i.e., areas point towards the sky. With this we certainly will save a lot of power and be able to customize the hardware for each customer at firmware level.
DVN: MicroVision as a leading innovator is surely thinking about and even preparing a next generation of automotive lidar sensor. What in your view will be core elements for next generation lidars: new and additional features, performance improvements or cost breakthroughs?
Sumit: I believe as the market matures and larger economy of scale is possible our future product roadmap will be ready to support. We certain see cost breakthroughs required to achieve 10’s of millions of units in future. To support this, we have concepts developed of a monostatic lidar with the same and perhaps higher performance criteria in place. Effectively instead of having a send and a separate receive path like we have today, we would be able to offer the performance in a product with a single optical path. This of course requires more customization of electronics components that are only feasible at higher economy of scales in silicon.
Additionally, we see our edge perception software to evolve further and provide object level sensor fusion of lidar and radar data streams as an important future key feature.
DVN: As a last topic of this interview, we would like to discuss more generally your vision about the evolution of the automotive lidar market. What is your estimation about the number of near range/mid-range/long range lidar sensors needed by the end of this decade on a premium vehicle?
Sumit: Our MAVIN product has been designed from the ground up to include near mid, and far field for the forward facing lidar in a single unit. To realize L3 high speed highway pilot features we believe 2 lidar per vehicle will be ideal. The rear facing lidar would require near and mid field performance only. A benefit of the lidar performance is that the number and sophistication of radar and camera sensors and required system calculation power can be reduced and system costs in fact will go down.
DVN: Which elements in your view can form the main three barriers for a fast market penetration and adoption of lidar sensors in automotive in the next years? How can they be overcome? Will there be regional differences between US, China, Japan, and Europe?
Sumit: The three main barriers will be sensor cost, low profile size and power. To overcome this is not rocket science fortunately. To contain cost, requires an established and reliable supply chain that OEM can verify and trust, as well as a technology which has proven scalability of cost with volume. To contain sensor size, requires innovative optical design with standard plastic and glass optics assembled on an automated active alignment line setup. This enables low profile sensors for roof line mounting. To contain low power, requires innovative features like smart pulsing and digital ASIC at 7 or 11 nm silicon nodes with object level interface implemented.
The regional difference would be at the OEM planning and manoeuvring software requirements. Our sensor is a measurement and edge perception device. We would provide clusters, tagged streaming point cloud and OEM software teams will control the l# ADAS features for their model for each region.
DVN: Dear Sumit, we thank you very much for this deep diving interview and we are looking forward to meeting you at one of our upcoming DVN lidar events again!!
- Get link
- X
- Other Apps
Comments
Post a Comment